Understanding Instrument Pipe Fittings: The Backbone of Efficient Systems
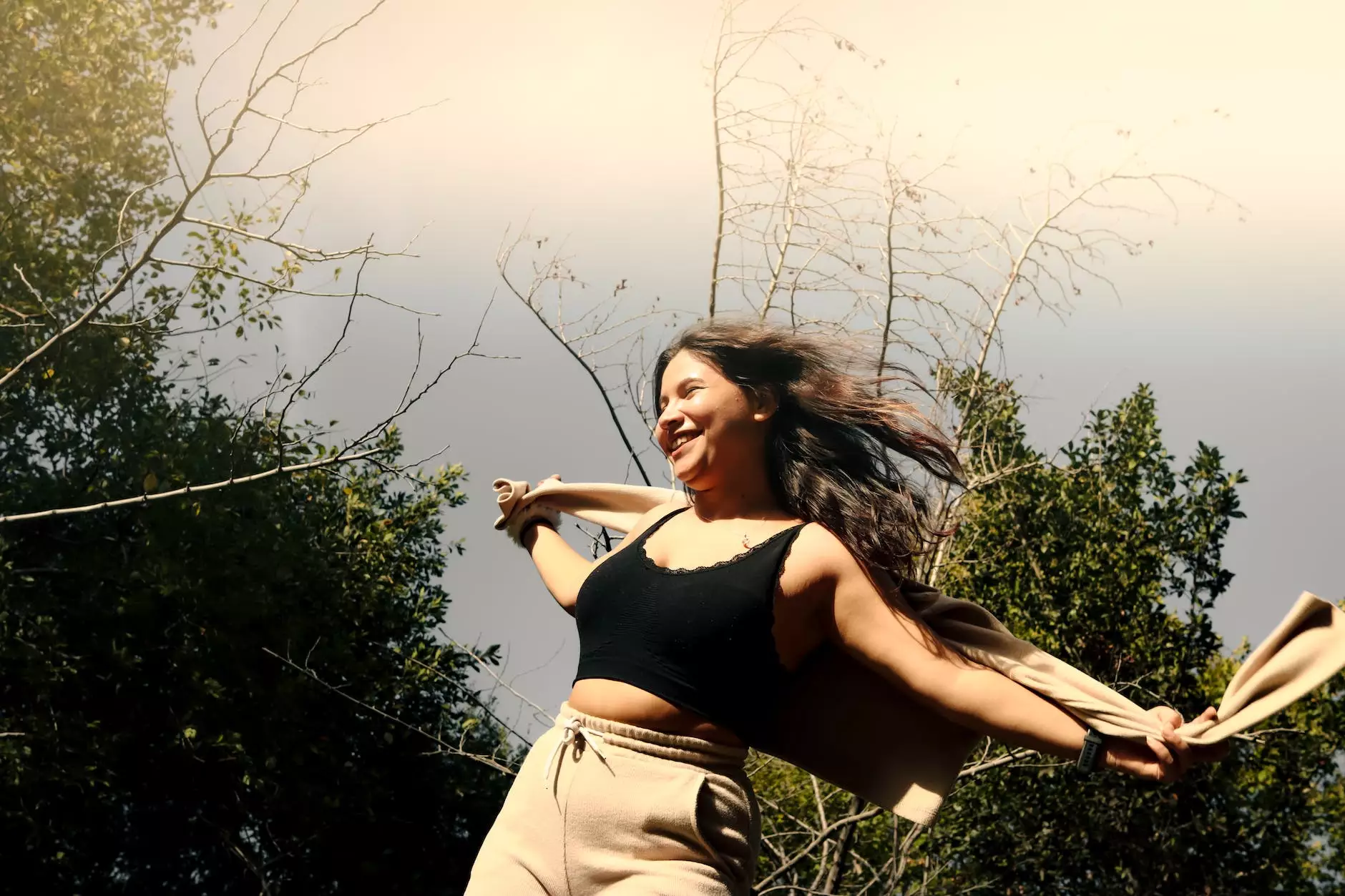
In the realm of industrial applications, instrument pipe fittings play a critical role in ensuring the seamless operation of various systems. These fittings are not just connectors; they are essential components that help maintain the integrity and functionality of pipelines in different industries including oil and gas, chemical processing, and water treatment. This article delves deep into the world of instrument pipe fittings, exploring their importance, types, materials, and practical applications.
The Importance of Instrument Pipe Fittings
Every industrial system that involves fluids or gases requires a network of pipes to transport these substances from one point to another. This is where instrument pipe fittings come into play. Without reliable fittings, the entire system can be compromised, leading to leaks, failures, and safety hazards. Here are several key reasons why instrument pipe fittings are crucial:
- Safety: Proper fittings minimize the risk of leaks and bursts, which can lead to hazardous situations.
- Efficiency: High-quality fittings ensure that systems operate smoothly without disruptions.
- Adaptability: Instrument pipe fittings come in various shapes and sizes, allowing customization for specific applications.
- Maintenance: Good fittings facilitate easier maintenance and repairs, reducing downtime and costs.
Types of Instrument Pipe Fittings
Instrument pipe fittings are categorized into various types based on their design and application. Understanding these types is essential for selecting the right fittings for your specific needs. Here are the most common types:
1. Elbows
Elbow fittings allow for the change of direction in piping systems. They are available in different angles, with 90-degree and 45-degree elbows being the most common. They help navigate around obstacles and connect various pipeline sections efficiently.
2. Tees
Tees are essential for creating branch connections in a piping system. They come in equal and reducing variations, allowing for seamless junctions where multiple pipes meet. This design enhances fluid flow and system flexibility.
3. Couplings
Couplings are used to connect two lengths of pipe together. They can be threaded or unthreaded and come in various sizes and materials, ensuring a secure and leak-free connection.
4. Crosses
A cross fitting connects four pipes at one junction, providing versatility in plumbing systems. This type is often used in complex piping arrangements where multiple pathways converge.
5. Reducers
Reducers allow for a change in pipe diameter within a system. They can be concentric or eccentric, optimizing flow rates and helping manage pressure changes effectively.
6. Caps and Plugs
Capped and plugged fittings are utilized to seal the ends of pipes, preventing flow through unused openings. This is particularly useful for maintenance or future expansion planning.
Materials Used in Instrument Pipe Fittings
The choice of material for instrument pipe fittings is vital to ensure durability, resistance to corrosion, and compatibility with the transported fluids. Common materials include:
1. Stainless Steel
Stainless steel is a popular choice due to its excellent corrosion resistance and strength. It is ideal for applications involving harsh chemicals and high temperatures.
2. Carbon Steel
Carbon steel is durable and cost-effective, making it suitable for high-pressure systems. However, it may require additional coatings to prevent rusting.
3. Brass
Brass fittings are often used in low-pressure applications and are favored for their machinability and resistance to corrosion.
4. Plastic
Plastic fittings are lightweight and resistant to a variety of chemicals. They are commonly used in water treatment and food processing applications.
Advantages of Using Instrument Pipe Fittings
Investing in high-quality instrument pipe fittings comes with numerous benefits:
- Longevity: Quality fittings reduce wear and tear, extending the life of your piping system.
- Cost-Efficiency: By preventing leaks and failures, you minimize repair costs and lost production time.
- Performance: Properly selected fittings ensure optimal flow rates and system efficiency.
- Compliance: High-quality fittings often meet industry standards, ensuring regulatory compliance and safety.
Choosing the Right Instrument Pipe Fittings
When selecting instrument pipe fittings for your business, several factors should be considered:
1. Application Requirements
Understand the specifics of your application. Consider factors such as temperature, pressure, and the type of fluid or gas being transported.
2. Material Compatibility
Ensure that the material of the fitting is compatible with the fluids it will contact. Use corrosion-resistant materials for challenging environments.
3. Size and Configuration
Select fittings that match the size and configuration of your existing piping system to ensure a seamless integration.
4. Regulatory Compliance
Verify that the fittings you choose meet applicable code requirements and industry standards.
Installation and Maintenance of Instrument Pipe Fittings
Correct installation is crucial for the efficiency and longevity of instrument pipe fittings. Here are essential tips:
1. Preparation
Before installation, inspect all fittings and pipes for damage. Clean all surfaces to ensure a proper seal.
2. Use Appropriate Tools
Utilize the correct tools for installation, such as wrenches, pliers, or specialized tools designed for specific types of fittings.
3. Follow Manufacturer Instructions
Always adhere to the installation guidelines provided by the fitting manufacturer to avoid potential issues.
4. Regular Inspections
Perform periodic inspections to identify signs of wear or damage early. Regular maintenance, such as tightening loose fittings, can prevent leaks.
Conclusion
In conclusion, instrument pipe fittings are indispensable in the world of industrial applications, ensuring safety, efficiency, and reliability in fluid transport systems. By understanding the types of fittings, their materials, and proper installation techniques, businesses can optimize their operations and minimize risks. Whether you're involved in oil and gas, chemical processing, or water management, investing in high-quality fittings from trusted suppliers like fitsch.cn can lead to significant long-term benefits. Prioritize quality and make informed choices to achieve maximum efficiency in your industrial infrastructure.