Unlocking the Potential of Low Pressure Casting in Business
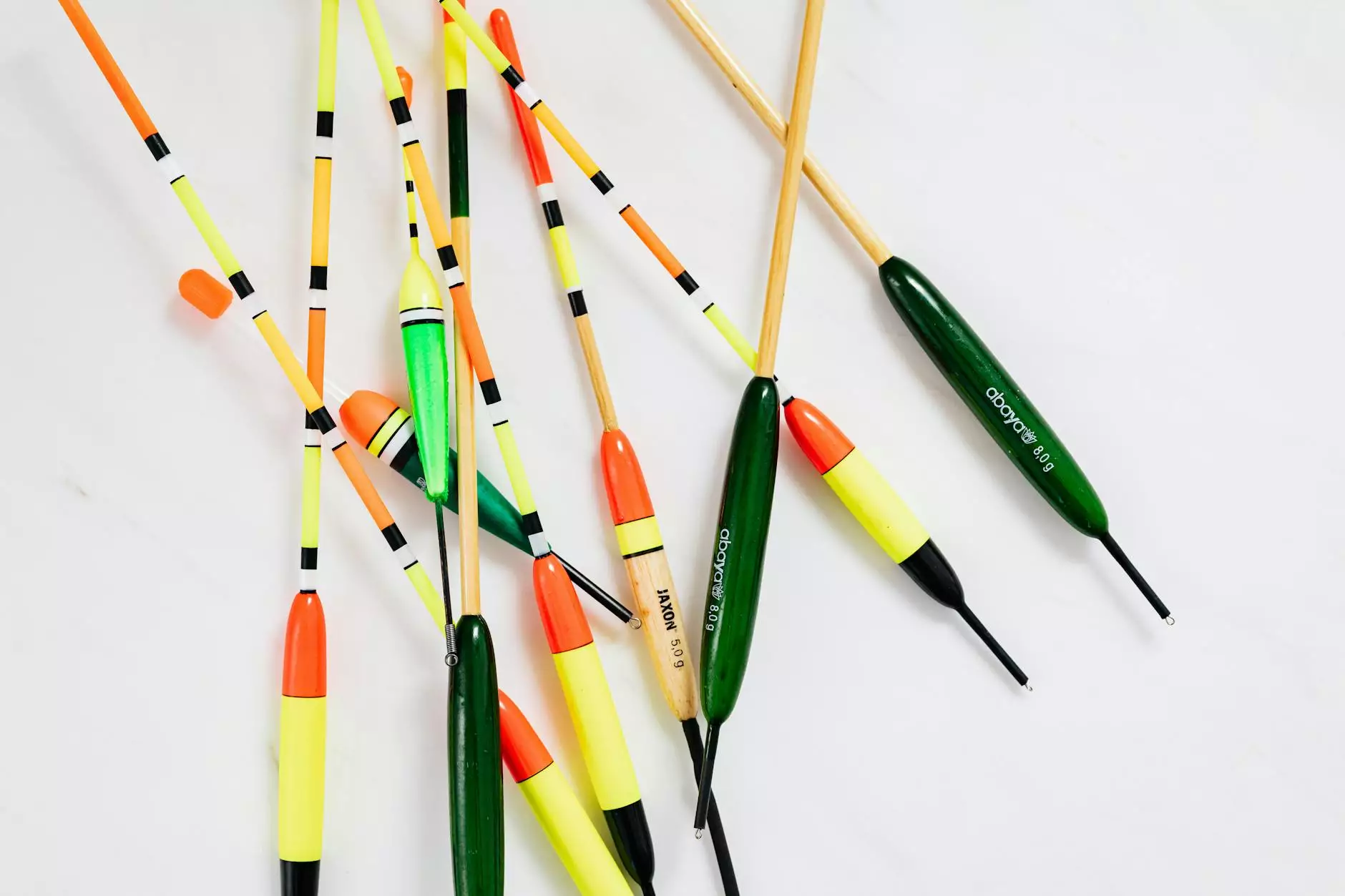
The world of manufacturing and design is evolving rapidly, and one of the significant innovations that has changed the game is low pressure casting. This process allows businesses to produce high-quality components with precision and efficiency. In this article, we will explore how low pressure casting can enhance various sectors, particularly in the realms of Art Supplies, Product Design, and 3D Printing.
What is Low Pressure Casting?
Low pressure casting is a casting technique that employs low pressure to force molten metal into a mold. Unlike traditional casting methods that rely on gravity, this method allows for more controlled filling of the mold, which can minimize defects and improve the quality of the final product. The benefits of low pressure casting have made it a popular choice in various industries, including automotive, aerospace, and consumer goods.
The Advantages of Low Pressure Casting
By utilizing low pressure casting, businesses can reap numerous advantages:
- Enhanced Quality: The use of low pressure results in improved mold filling, reducing the likelihood of air entrapment and enhancing the mechanical properties of the finished product.
- Improved Surface Finish: The method provides a better surface finish, which is particularly beneficial for products that require a polished look without extensive post-processing.
- Material Efficiency: Lower waste generation and more efficient use of materials make low pressure casting a sustainable option for manufacturers.
- Faster Production Cycles: Reduced cycle times mean that products can be brought to market quicker, giving businesses a competitive edge.
Low Pressure Casting in Art Supplies
In the domain of art supplies, low pressure casting can revolutionize the way artists and designers create their products. The ability to produce detailed and intricate shapes opens up new possibilities for artistic expression. Here are some ways low pressure casting is being utilized in the art supplies industry:
Creating Sculptures and Decorative Items
Artists can create intricate sculptures using low pressure casting by pouring molten materials into specially designed molds. This process allows for replication of complex designs with high fidelity, enabling artists to share their creations with a wider audience. The durability of metal castings also ensures that these pieces can withstand the test of time.
Custom Tools and Accessories
Low pressure casting allows for the production of custom tools and accessories tailored to the specific needs of artists. This might include bespoke handles for brushes, ergonomic grips for sculpting tools, or even unique palettes that enhance the creative process.
Low Pressure Casting in Product Design
In the realm of product design, the applications of low pressure casting are vast and varied. Designers can take advantage of this technology to create prototypes quickly and cost-effectively. Let’s delve into some specific applications:
Rapid Prototyping
Low pressure casting is pivotal in the rapid prototyping stage of product development. Designers can create prototypes that closely resemble the final product in terms of material properties and aesthetics. This aids in refining designs and making informed decisions early in the development process.
Functional Components
Many consumer products require functional metal components, and low pressure casting can produce these parts with precision. This includes items like brackets, housings, and other essentials that must meet specific engineering requirements.
The Role of Low Pressure Casting in 3D Printing
As the demand for 3D printing capabilities continues to rise, integrating low pressure casting opens new avenues for innovation. Here's how these technologies converge:
Combining Techniques
3D printing can be used to create molds for low pressure casting, enabling designers to experiment with complex shapes and geometries that may be difficult to achieve through conventional methods. This synergy maximizes creative freedom while maintaining the advantages of high-quality metal castings.
Production Scalability
For businesses looking to scale their production, combining low pressure casting with 3D printing allows for efficient production runs. Small batches can be produced at a lower cost and higher quality, catering to customized market demands.
Implementing Low Pressure Casting in Your Business
For businesses considering the adoption of low pressure casting, it’s essential to evaluate several aspects before implementation:
Assessing Needs and Capabilities
Businesses must first analyze their specific needs regarding product design, material requirements, and overall production goals. Understanding these elements will help in selecting the right equipment and materials.
Investing in Technology
Investing in advanced casting technology is critical. This includes choosing the right casting machines, molds, and materials that can withstand the demands of low pressure casting. Collaborating with experts in the field can lead to more informed decisions and better outcomes.
Training and Development
Ensuring that staff are adequately trained in the low pressure casting process is essential for maximizing productivity and product quality. Continuous learning and adaptation will keep businesses on the cutting edge of industry advancements.
Conclusion
Low pressure casting is an incredible technique that offers various benefits across multiple industries, including Art Supplies, Product Design, and 3D Printing. By understanding and leveraging this innovative process, businesses can enhance their product offerings, improve efficiency, and stay competitive in an ever-evolving market.
As we move towards a future where quality and speed are paramount, embracing technologies like low pressure casting will undoubtedly be a key driver of success. Companies willing to invest in this transformative process will find themselves at the forefront of their respective fields, creating exceptional products that resonate with customers.